ABOUT
X-One V2 is the real meltable resin developed and produced by BlueCast for DLP and Monochromatic LCD machines. Thanks to the low temperature melting polymer it ensures smooth surface finish and perfect lettering. X-One was developed by BlueCast in order to allow perfect casting results with any kind of investments and burnout cycles. It is the first castable resin with 0% shrinkage and an extreme dimensional stability.
X-One V2 UPGRADES
- Same print profiles as version V1
- Improved resolution, especially for the new 12k printers. Better accuracy and reduced bleeding.
- Enhanced printability, particularly for DLP technology (no need for additives).
- Increased stability at low temperatures.
- Improved meltability for micro-details and engravings.
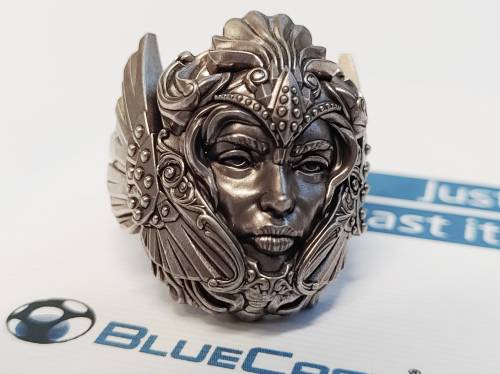
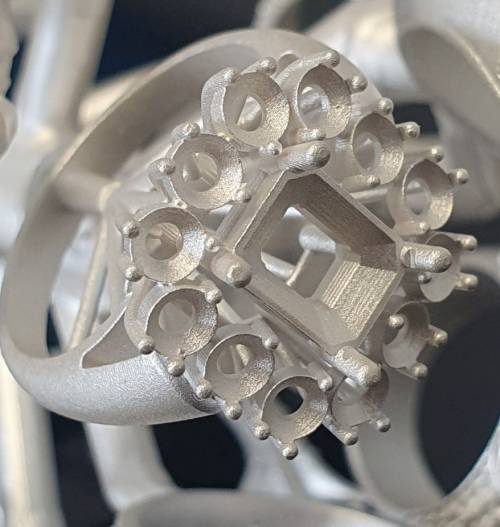
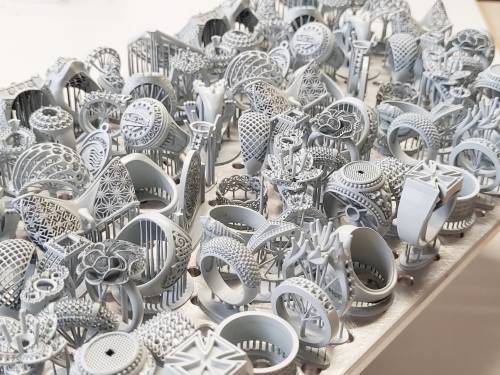
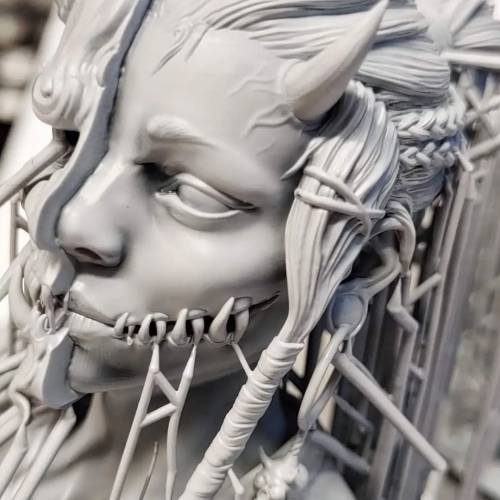
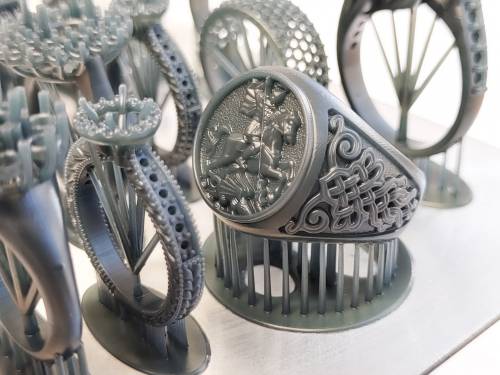
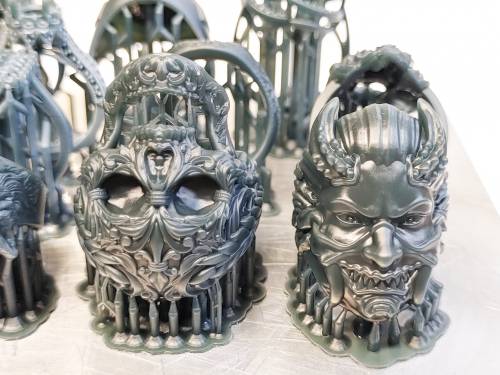
�
HOW TO USE IT
CRAFTEN X-ONE
BEFORE PRINT
- Due to the use of a low-temperature melting polymer, the resin solidifies below 18°C. Prior to use, it is necessary to heat the resin within the temperature range of 25 to 40°C. The optimal operating range is from 20 to 30°C. The resin will remain in liquid form at temperatures above 18°C.
- Various methods can be used to heat the resin, such as microwave ovens (never exceeding 30 seconds), ultrasonic cleaners, hot air, baby bottle warmer, etc.
- Before pouring the resin into the resin tank, shake the bottle for one minute.
- For proper debubbling, allow the resin to rest in the resin tank for 5 minutes before starting the print. To expedite the process, the resin can be filtered to remove air bubbles or vacuumed from the opened bottle.
- Due to the use of a low-temperature melting polymer, the minimum supports (the initial pattern supports) must be larger than usual. The ring sprue can be designed within the model and used as the main support.
- Avoid using contact points under 0.4 mm and ensure proper support for the shank of the rings.
- Failure to filter the resin after each print or neglecting to heat the resin before each print may result in printing failures. Do not store the resin in the tank. Please remove the resin from the printer tank, filter it, and store it in the original bottle. For maximum detail, consider using HD FEP or No-FEP - PFA.
POST-PRINTING CLEANUP
- Patterns printed with this resin are more fragile compared to other BlueCast resins, particularly delicate patterns like filigree and prongs. Handle them with care.
- The resin contains a waxy polymer, making the patterns moderately softer.
- Clean the prints using 91% to 99% ethyl alcohol.
- When using an ultrasonic cleaner, run a 5-minute cycle with heat turned off (recommended procedure).
- With a resin washer machine, run a cycle of approximately 5 to 10 minutes.
- For simple immersion in an alcohol bath, wait approximately 10 minutes submerged.
- When using IPA alcohol, reduce the washing time.
- After washing, dry the patterns using compressed air. The resin color will transition from dark gray to light gray/white.
- After the initial washing step, spraying brand new 91% to 99% ethyl alcohol or IPA onto the patterns and drying them again will improve the casting quality.
- If compressed air is unavailable, a hairdryer can be used to dry the patterns.
- Whitening of the resin will require longer times.
- The duration of resin whitening is strongly influenced by the quality and exhaust of the alcohol used, as well as the washing procedure. Lower quality and more exhausted alcohol will require longer whitening times.
- After the washing procedure, allow sufficient time for the alcohol to evaporate before investing. Post-curing can expedite alcohol evaporation, making the patterns more rigid and stiff.
ULTRA FAST BURNOUT ALLOWED
- The ultra-fast burnout (2 hours at 700°C) has been validated for X-One and X-Filgree V2 only.
- Allow the flask to rest for 3 hours, then proceed to 700°C (1290°F) and maintain that temperature for 60 to 90 minutes.
- Reduce the temperature to your casting temperature and hold for 60 minutes before casting as usual.