ABOUT
BlueCast X10 is the evolution of our well known X5 polymer and it is useful for direct investment casting of jewelry and dental patterns. It is a resin developed to give perfect casting using wax equipment as well normal gypsum bonded investments. An 80% wax-like filled photopolymer for reliable casting with zero ash content and clean burnout, highly accurate resin captures intricate features and offers the smooth surfaces. Its formulation is suitable for jewelry where huge quantity of metal is needed and/or high details are required.
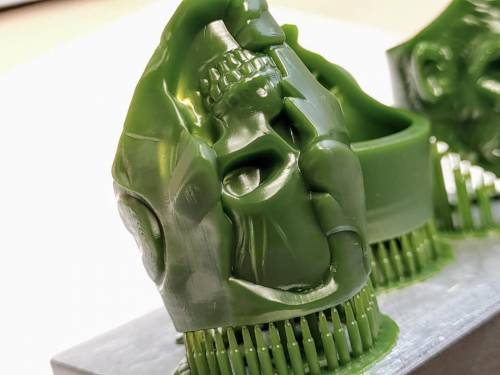
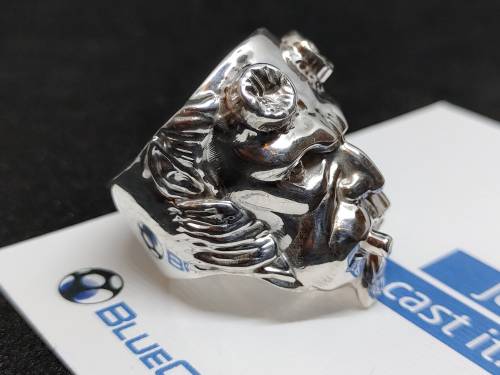
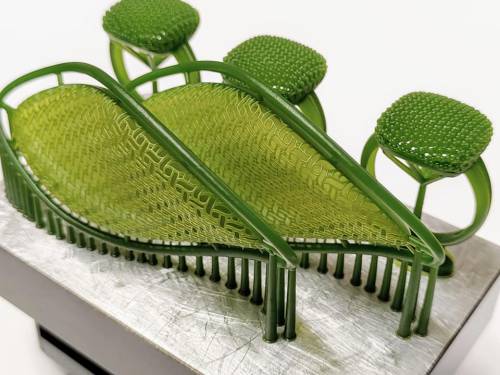
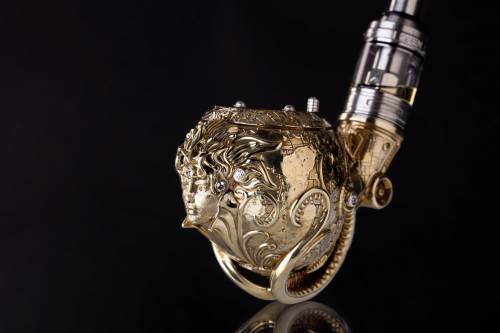
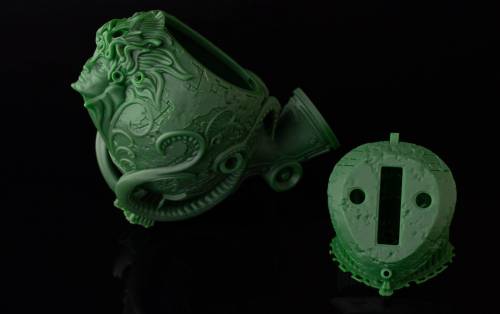
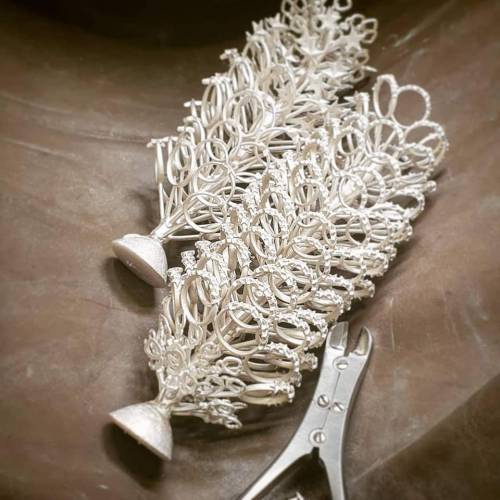
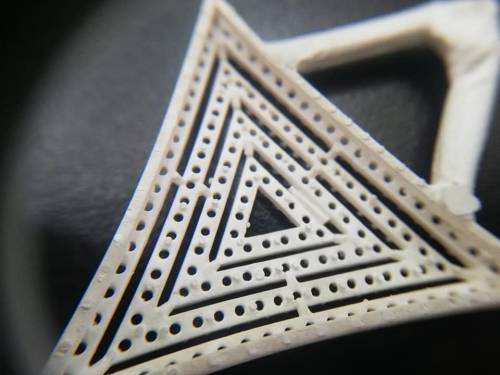
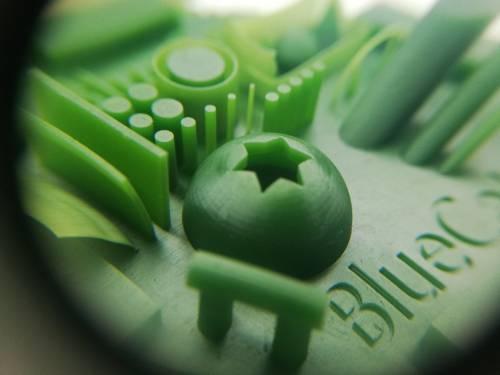
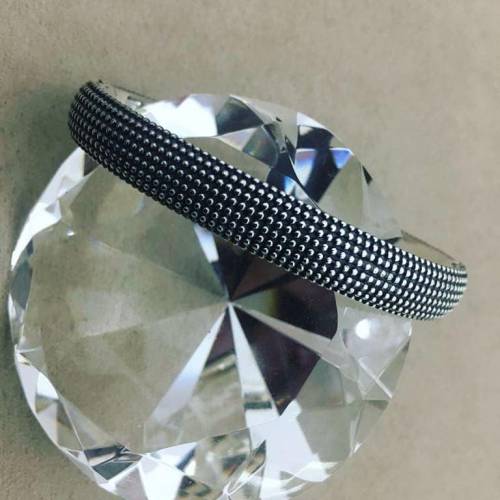
�
HOW TO USE IT
CRAFTEN X10
BEFORE PRINT
- If you own a 4K or 8K printer, we strongly suggest using one of the X-10 additives to increase resin resolution and customize the resin according to your needs (Sharpenizer – Hardenizer - Softenizer).
- Before use, shake the resin bottle for 60 seconds. If the resin has been sitting in the tank, use a silicone spatula to ensure thorough mixing. In case of specific climatic conditions, such as a room temperature below 20°C, it is recommended to preheat the resin.
- If the resin has been sitting in the tank, use the silicon spatula to ensure thorough mixing.
- It is suggested to filter the resin before each use to avoid any damage to the LCD screen. Use the PrimerCat primer to improve resin adhesion to the platform.
- Apply 2 or 3 drops to the print platform and spread them with a spatula until achieving an invisible and homogeneous film.
- It is also recommended to pre-scale the model by +3% to compensate for resin shrinkage.
POST-PRINTING CLEANUP
- Clean the prints by pouring 91% or 99% IPA or ethyl alcohol for approximately 1 minute.
- Dry and clean the pieces using compressed air for best results.
- In-house casting:
- UV curing is not necessary
- It is advisable to invest within 12 hours after the print. - Casting by service::
If relying on external casting services:
- Rescale the file model up to +2% before printing.
- Perform standard cleaning with alcohol and drying with compressed air (as indicated previously).
- UV cure until the model is completely white/clear.
FAST BURNOUT ALLOWED
- The ideal temperature for fast burnout of BlueCast X10 resin is 780°C or 1436°F.
- To achieve fast burnout, it is necessary to use investment materials capable of withstanding temperatures above 780°C. We recommend using high-quality investment materials.
- For a fast burnout schedule, allow the flask/investment to stand for at least 120 minutes. Preheat the kiln to 760-780°C (1400-1436°F), then insert the cylinder and maintain a constant temperature for 120/180 minutes. Reduce the temperature to your casting temperature and hold for 60 minutes before casting as usual.
- During the initial burnout, turn the flask on its side, and then turn it with the button facing up for the rest of the cycle to ensure good airflow.